Countless news articles and many non-governmental organizations (NGOs) would seem to agree—single-use plastic is the current poster child for everything wrong with stewardship of our planet. Ocean waste, damaged marine life, barges adrift with unrecycled plastics and clogged landfills—all are indicative of the plastics problem—or what might be better described as a plastics contradiction.
With waste piling up, there has been a surge in interest for more traditional packaging alternatives, those materials that plastics replaced over the last few decades—paper, glass and metals. However, all these plastic-free options have a significantly higher carbon footprint than most plastics, even when substantial recycled material is used.
While paper fares best in virgin manufacture, plastics manufacture emissions are about three-quarters of that of glass and half that of aluminum. In recycling processes, however, plastics beat them all, with less than one-tenth the emissions of glass, one-fourth that of paper and one-third that of aluminum.
There are other less recognized benefits of plastics, too. Lately, polymers have received attention for their impact on public safety, providing material for masks, gloves and food packaging to prevent disease transmission. In fact, materials used as inputs for medical equipment and supplies average about 50 percent plastics.
Asking the right questions
Many ideas to solve the plastic crisis are being put forward. However, before getting behind the latest national or local initiative, it is important to understand more about this issue from a materials point of view.
The debate about how to attack this challenge and what areas to focus on is muddied by which statistics people use. For instance, microplastics found in the ocean are predominantly from the breakdown of plastic waste already there, but the wear of car tires and washing of synthetic clothing provide large amounts as well.
Likewise, the widespread use of plastic straws (Americans use millions a day) highlights human complicity in this issue, but that’s tiny in comparison to the plastics entering the oceans from Chinese and Indonesian rivers and beaches.
What is clear throughout this debate: there are material alternatives to many of the options for single-use plastics, though each has limitations and challenges, whether in performance, cost or environmental impact.
In this era of responsible business, chemical companies are uniquely positioned with the R&D capabilities, long-standing spirit of innovation and manufacturing capacity at scale to be part of the solution and lead the shift to the circular economy.
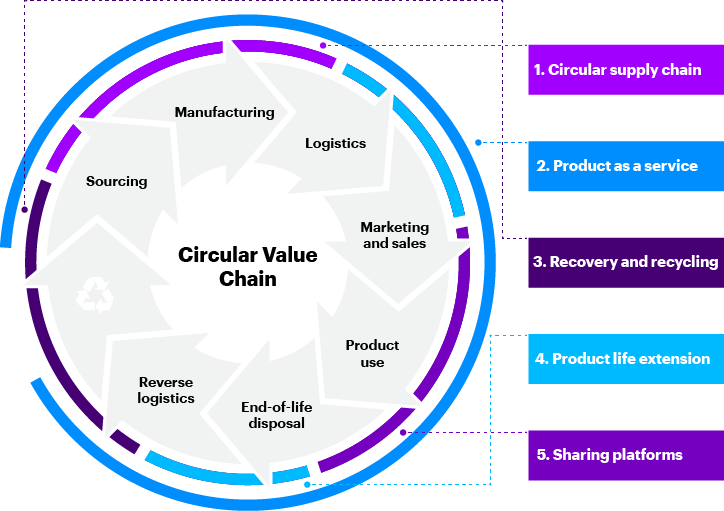
Exploring solutions
Responding to changing demands for eco-friendly alternatives requires a three-fold strategy: 1) exploring new materials for consumer products and packaging, 2) adopting new processes and 3) embracing new business models that meet society’s sustainability requirements. The companies that drive this shift can unlock newfound chemical industry growth.
Exploring new materials
Ironically, the current push for a plastic-free future does not mean all plastics: bioplastics tend to be given a free pass, but this is where it gets a little complicated. Some bioplastics degrade relatively quickly in the ocean; some are compostable; some need an industrial facility to do so rapidly; and some are as durable as the foamed polystyrene food packaging that is likely to last 300 years before breaking down fully. In other words, bioplastic does not always mean biodegradable.
Currently, there are only a few marine degradable plastics available (defined as those that break down completely within a year in seawater) that can help solve some of our ocean waste challenges. But potential success stories do exist. Take cellophane, which is synthesized from wood, and used to package candies, tea and other food products. Even metallizing the cellophane to create a light and oxygen barrier does not stop it from being compostable.
Another class of plastics that are quickly degradable in seawater are polyhydroxyalkanoates (PHAs) and polyhydroxybutyrate (PHBs) derived from bacteria that feed on sugary sources such as corn. Resins are being developed for a range of single-use as well as durable applications. There is also additive technology to allow molecular disintegration of conventional polymers without losing properties for its intended use, such as Timeplast.
The current challenge for PHA/PHB bioplastics is the price of sugar, since it takes four pounds of sugar to produce one pound of the plastic. Thus, the plastic has a base-level cost that is higher than all the commodity plastics it is competing against. Fortunately, recent advances in raw material compatibility has enabled NAFIGATE to produce a version of this plastic, known as P3HB, from the microbial fermentation of waste cooking oil, removing the high cost of the raw material entirely.
Some starch-based bioplastics, such as NuplastiQ from BiologiQ,5 a carbon neutral resin, are able to work with existing petroleum-based commodity plastics. Creating a blend of up to 20 percent reduces the quantity of non-renewables and renders them less persistent in the unfortunate case they end up in the environment. This blending still allows for both mechanical and chemical recycling of the blended plastic and actually improves certain characteristics such as strength while retaining shelf stability. These drop-in solutions do not require any changes to existing processing of plastics such as polypropylene, polyethylene and polystyrene.
Adopting new processes
Petrochemical producers are among the most sophisticated in terms of managing in-process hydrocarbons flows, using a mix of products and technologies. They are often connected with refineries that can both feed chemical units or use their streams for fuel manufacture or energy production. While they have often been on the sidelines of new plastics-waste solutions, they are now becoming “awakening giants” that can use their hardware and technologies to mitigate waste issues, at a scale significantly larger than most plastics recycling companies.
The hydrocarbon pool can be viewed from a holistic perspective as well, encompassing all hydrocarbon sources. For instance, the Btu content of organic trash going to landfills in the U.S. is equivalent to the 22nd largest oil producer’s (India) annual production—865,000 barrels of crude oil equivalent per day. This waste includes plastics (single-use and durable-use), food, yard trimmings, paper, textiles, rubber and other hydrocarbon products. All this waste presents an enormous opportunity.
One solution can be found in scale circular integration, where some level of processed/unprocessed waste is diverted from landfills and shipped to integrated refining/petrochemical sites to get sorted, cleaned and ground according to various requirements for optimal value and flow. Here, various waste-to-chemicals/fuels processes can be employed and incorporated into the complexes. New technologies and software for sorting waste (like infrared and near-infrared laser sensors/detectors), artificial intelligence (AI), machine learning and other Industry X.0 technologies can go far in helping to scale these capabilities.
Embracing new business models
The impact of using new products (bio-based, degradable, etc.) or processes have strong business model implications. Bio-based products would need a completely different supply chain based on feedstock alone. The location of manufacturing plants, seasonal buying patterns and varying price drivers and swings (e.g., oil price drops would add price pressures, etc.) implies new supply chain processes and systems, too.
For scale circular integration, the technology already exists, but the biggest hurdle is the supply chain. Strong collaboration is necessary, especially between integrated petrochemical companies, waste handling companies and government. Collection may occur just as it currently does with some sorting at current garbage dump sites/landfills and then transportation to refineries via barge, rail or truck.
Another way forward is revitalizing a business model of the past: to bring back the method of milk delivery but for all our consumables. Imagine regular distribution of food, health, beauty and other everyday items in durable containers, which consumers can send back to be washed, refilled and delivered again. TerraCycle7 is doing this now with an offering called Loop8 that partners with brands and stores to make doorstep delivery of hundreds of items that are packaged in reusable containers—often made of glass and metal—that can withstand high temperature cleaning.
Returning to value
Improving waste collection systems, especially in Asia, would go far in solving the waste issue. But landfill and emissions challenges remain. What has been lost in consumers’ drive toward convenience has been the value of the materials that they use. People easily forget the engineering marvel and inherent value of a carbonated beverage bottle.
Although revolutionary from a materials perspective, today’s plastic is a problem that society has a responsibility to solve. It’s time to pursue innovative circular economy solutions. The value of plastic should not be just the raw material cost of the petroleum-derived chemicals it is produced from, but also the impact it will have when not brought back into the material stream via recycling or strategic composting.
It is undeniably the case that it is society’s collective responsibility to treat the objects we use daily with the respect they deserve. And for chemical companies, now is the time to take the next bold step into the future, harnessing product and process innovation to bring additional value to materials, responsibly reduce waste and lead the shift to the circular economy.
This article originally appeared on accenture.com